
Updates
Flexographic printing onto polythene
Jan 16, 2025
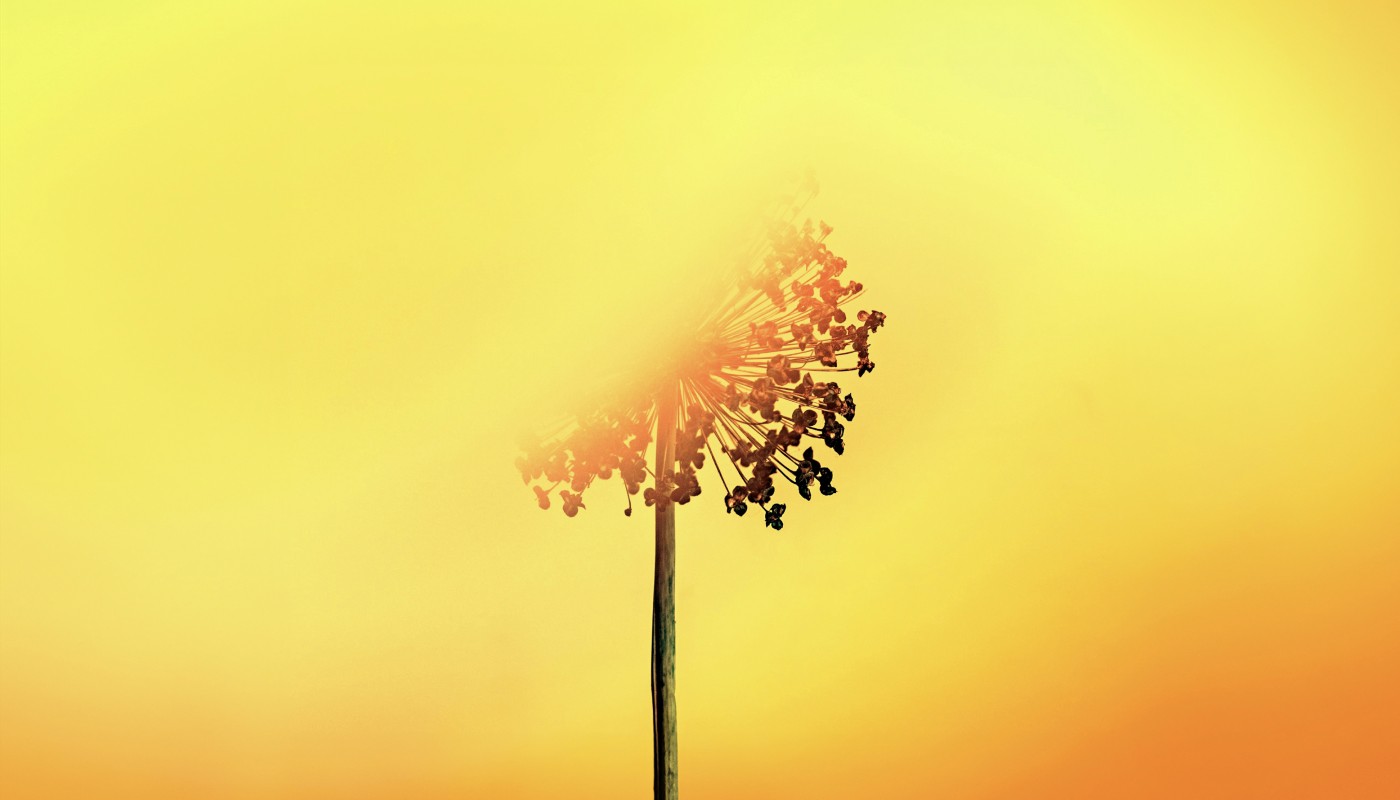
Flexographic Printing on Polythene: The Art and Science Behind Custom Packaging
In the competitive landscape of modern packaging, product presentation has never been more important. While the structural integrity of packaging protects products, it's the print on that packaging that communicates brand identity, product information, and often drives purchasing decisions. For polythene packaging, flexographic printing stands as the definitive technology delivering high-quality, cost-effective printing solutions across industries ranging from agriculture to retail.
The Fundamentals of Flexographic Printing
Flexographic printing—often shortened to "flexo"—is a direct rotary printing process that uses flexible photopolymer plates mounted on fast-rotating cylinders. While its roots date back to the early 20th century, today's flexographic printing bears little resemblance to its primitive ancestors, having evolved into a sophisticated, highly automated process capable of producing exceptionally precise results on polythene films.
The basic mechanics of flexographic printing follow a relatively straightforward sequence:
Ink delivery: A precision-engineered anilox roller with microscopic cells collects ink from a reservoir
Ink metering: A doctor blade removes excess ink from the anilox surface, leaving ink only in the cells
Plate impression: The anilox roller transfers ink to raised areas on the flexible printing plate
Substrate contact: The inked plate transfers the image to the polythene film as it passes between the plate cylinder and impression cylinder
What distinguishes modern flexography from other printing technologies is its remarkable versatility across substrates. While many printing techniques struggle with non-absorbent materials like polythene, flexographic printing has been optimised specifically for these challenging surfaces.
The Technical Precision Behind Flexo on Polythene
Printing on polythene presents unique technical challenges that flexographic technology has been specifically engineered to overcome. The non-porous nature of polythene means inks cannot be absorbed as they would on paper substrates. Instead, they must form a mechanical bond with the treated film surface.
This process begins with surface treatment—typically corona discharge or plasma treatment—which microscopically alters the polythene surface, creating anchor points for ink adhesion. Without this crucial preparation, inks would simply sit on the surface, easily smudging or scraping off during handling.
The inks themselves represent another marvel of modern chemical engineering. Solvent-based, water-based, and UV-curable inks each offer different advantages:
Solvent-based inks provide excellent adhesion and abrasion resistance, making them ideal for industrial packaging. This is what we use for printing at Modern.
Water-based inks offer environmental benefits and reduced VOC emissions
UV-curable inks deliver exceptional color vibrancy and immediate curing through photopolymerization
The precision of modern flexographic presses is equally impressive. With registration accuracy measured in microns, today's equipment can maintain color-to-color alignment with remarkable consistency throughout long production runs. This precision enables the reproduction of fine text, barcodes, and intricate graphics that would have been unimaginable in earlier generations of flexo technology.
Color Management and Print Configurations
For brand owners, color consistency is paramount. Modern flexographic printing on polythene employs sophisticated color management systems to ensure that brand colors are reproduced with remarkable consistency across different print runs and even different facilities.
Most flexographic printing on polythene (layflat tubing) employs one of several standard configurations:
1+3 configuration: One color on the back, three colors on the front
2+2 configuration: Two colors on each side
4+0 configuration: All four colors on a single side
These arrangements offer different advantages depending on the packaging requirements. For example, a feed bag might use a 1+3 configuration with product information on the outside and simple handling instructions on the inside, while retail packaging might utilize all four colors on the external surface for maximum visual impact.
Color sequence also plays a crucial role in image quality. By strategically arranging process colors (cyan, magenta, yellow, and black) along with any spot colors, printers can maximize color gamut while minimizing the moiré patterns that can occur when printing halftones.
The Role of Prepress in Print Quality
While the printing press receives most attention, much of the magic in flexographic printing happens before the job reaches the press floor. Modern prepress workflows include:
Digital artwork preparation: Optimising designs for the flexographic process
Colour separation: Breaking artwork into printable colour channels
Plate imaging: Exposing photopolymer plates through digital mask technologies
Distortion calculation: Compensating for the natural distortion that occurs when printing on flexible films
The development of digital platemaking technologies has revolutionized flexographic printing quality. High-definition flexo plates now feature microstructured surfaces that facilitate cleaner ink transfer and superior dot reproduction, enabling print quality that rivals more expensive printing methods.
Screening technologies have similarly advanced, with stochastic (FM) screening and hybrid AM/FM screens enabling smoother gradients and sharper details while reducing the visibility of screening patterns that once limited flexographic quality.
Applications Across Industries
The versatility of flexographic printing on polythene has made it indispensable across diverse industries:
Agriculture: Flexo-printed feed bags and seed packaging combine durability with clear product identification and planting instructions. The ability to print legible text even on textured, heavy-duty films makes flexo ideal for the challenging conditions of agricultural environments.
Construction: High-contrast printing on rubble sacks and aggregate bags ensures safety information and product details remain visible in dusty construction environments. Abrasion-resistant inks ensure this information remains legible throughout the product lifecycle.
Retail: The exceptional color reproduction of modern flexo creates eye-catching packaging that stands out on crowded retail shelves. The ability to print on lightweight films economically makes flexo the natural choice for high-volume consumer goods packaging.
Industrial: For component packaging and industrial supplies, flexo delivers clear, durable printing of part numbers, specifications, and handling instructions—critical information that must remain legible in demanding industrial environments.
Environmental Considerations
The environmental impact of packaging printing has come under increasing scrutiny, driving significant innovations in flexographic technology. Modern developments include:
Solvent recovery systems that capture and reuse volatile organic compounds
Water-based ink systems that dramatically reduce VOC emissions
Energy-efficient UV LED curing that reduces power consumption
Thin plate technologies that reduce photopolymer waste
These advances have transformed flexographic printing into one of the more environmentally responsible printing processes available for polythene packaging, especially when combined with the thin-gauge films made possible by modern extrusion technology.
Quality Assurance in Flexographic Printing
Maintaining consistent print quality requires sophisticated monitoring throughout the printing process. Modern flexographic presses incorporate inline quality control systems that can:
Monitor registration to detect and correct misalignment between colors
Inspect print quality using high-resolution cameras to detect defects
Verify barcode readability to ensure compliance with retail requirements
Check color accuracy against established standards
These automated systems allow press operators to maintain exceptional quality standards even at the high production speeds that make flexographic printing so economical.
The UK Advantage in Flexographic Printing
For businesses sourcing printed polythene packaging in the UK, local manufacturers offer several distinct advantages. Beyond reduced shipping times and carbon footprint, UK printers provide greater flexibility in run lengths, accommodating both high-volume standardised packaging and shorter runs of specialised or seasonal packaging.
UK printers also offer closer collaboration throughout the design process, allowing packaging engineers to provide input that ensures designs are optimised for the flexographic process. This collaborative approach often results in superior print quality and reduced production costs.
Future Trends in Flexographic Printing
The evolution of flexographic printing continues with several emerging technologies poised to further enhance quality and efficiency:
Extended colour gamut printing that uses a standardised set of 7 colours to reproduce a wider range of spot colours without ink changes
Fixed palette printing that dramatically reduces press setup times and ink inventory
Automated registration systems that reduce makeready time and material waste
Digital workflow integration connecting design, prepress, and production in a seamless information flow
These innovations promise to further strengthen flexography's position as the optimal printing technology for polythene packaging.
Conclusion
Flexographic printing on polythene represents a remarkable convergence of mechanical engineering, polymer chemistry, and digital imaging technology. For businesses seeking to enhance their packaging with high-quality printing, understanding the capabilities and advantages of this process is essential to making informed decisions.
From the technical specifications of the printing plates to the chemistry of the inks, every aspect of the flexographic process has been optimised for printing on challenging substrates like polythene. The result is a printing method that delivers exceptional quality, durability, and cost-effectiveness across applications ranging from simple industrial markings to complex retail packaging.
By choosing manufacturers with advanced flexographic capabilities, businesses can ensure their packaging not only protects their products but also communicates effectively with end-users—transforming utilitarian polythene into a powerful marketing and information tool.
Modern Flexible Packaging Ltd offers custom flexographic printing on polythene with up to 4 colours in various configurations. Contact our Nottingham facility to discuss your printed packaging needs.